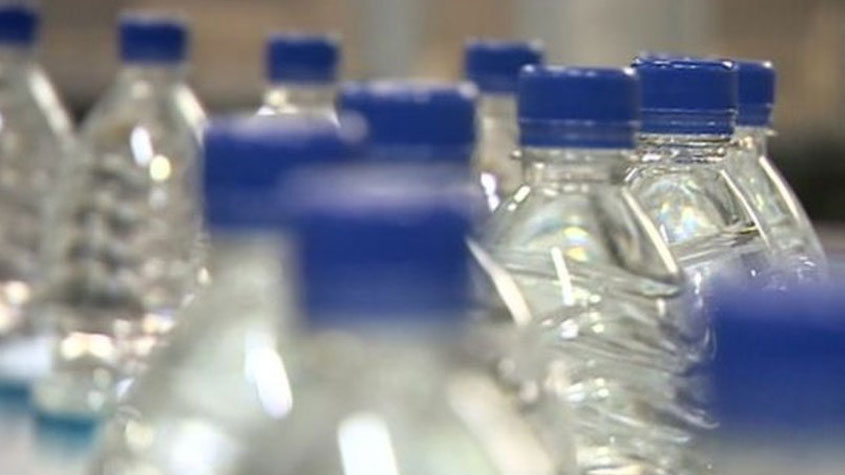
The food and beverage industry is playing a key role in reducing the carbon footprint by using more recycled content in packaging and increasing material recyclability, says Angelica Buan in this report.
Rising consumer awareness on environment protection is a catalyst for government regulations such as levying taxes on plastics use and global initiatives to reducing packaging wastes.
Less packaging not only equates to less generation of waste and energy use; it also means cost savings for manufacturers and consumers. Using post-consumer recycled (PCR) resins, downsizing and the use of renewably sourced materials are effective ways of reducing packaging.
The food and beverage industry, which dominates the market share for packaging, is a critical sector in the packaging sustainability circuit. It is forecast to cross US$173 billion by 2025, according to a Grand View Research report.
The increasing adoption of recycled PET or rPET is thus an important leap in creating a waste-free ecosystem that benefits both producers and consumers, since rPET is clean and safe and due to its versatile benefits. Recycling PET bottles has also been found to consume less energy than producing new ones. Technologies are also available to facilitate recycling, and thus are aiding in the growth of the rPET market.
Bottled water overhauled with rPET use
A number of beverage and bottled water producers are redesigning their packaging in bid to adopt sustainability into their brands.
Nestlé Pure Life is launching a new 700 ml bottle made from 100% food-grade rPET throughout North America. Nestlé says that the release of the new bottle demonstrates the brand’s commitment to reducing its carbon footprint. Since 2005, the company has reduced the amount of PET plastic in Nestlé Pure Life half-litre bottles by 40%, and has initiated to reduce waste and materials in packaging across its portfolio of beverages. More recycled plastic will be introduced into its beverage range in the coming years, it said.
Through global alliances such as the Trash Free Seas Alliance, founding of the bio-PET NaturALL Bottle Alliance, and investments in large-scale organisations like Closed Loop Fund, Keep America Beautiful and start-ups like RecycleUp, Nestlé Waters said that it is collaborating with stakeholders across the PET value chain to create shared solutions to one of the world’s most pressing environmental issues.
Meanwhile, French mineral water brand Evian is committed to using 100% rPET bottles by 2025, whereby all bottles will be made from recycled plastic without the need for any virgin plastics. This will enable plastics to evolve from a potential waste to become a valuable resource, the company said.
Currently, Evian bottles are recyclable and globally contain on average across the range 25% rPET. In order to achieve its 2025 goal, Evian is partnering with technology companies such as Loop Industries, which has developed a technology that enables a continuous loop for recycling on a large scale and transforming all types of PET plastic waste into the high-quality plastic required by Evian.
For its part, global packaging company Sonoco is committing to achieve packaging sustainability and recycling in support of the food industry’s efforts to reduce global food waste. In its 2018 corporate responsibility report, it has highlighted sustainable use and increased recyclability of packaging by 2025. Specifically, it said that it will increase the equivalent by weight from 75% to 85%, the amount it recycles, or causes to be recycled, relative to the volume of packaging it places into the global market place. It is also increasing the use of PCR resins in its plastic packaging from 19% to 25%. Furthermore, the company says it will ensure that approximately 75% of its rigid plastic packaging can carry the relevant on-package recyclable claim.
In addition, Sonoco adds that it will not use resin additives that purport to degrade in landfills or waterways by simply breaking up into smaller pieces. Finally, the company says it will ensure all of its production facilities using plastic pellets have systems to prevent discharges into the environment.
Sonoco has committed nearly US$3 million to Clemson University to create a joint initiative called SonocoFRESH. It is also a joint development partner in Florida’s Plant City, which is focused on improving the supply chain for fresh produce by connecting harvesting technology with new packaging technology.
PCR in food packaging
An efficiently designed packaging ensures that reduced use of plastic does not compromise performance and functionality of the packaging. This is proven by already a growing number of packaging manufacturers that are developing rPET-based packaging.
UK-based flexible packaging and lidding films supplier, KM Packaging, has developed a new, resource efficient, reduced-plastic packaging for its KPeel range of lidding film solutions. The mono-PET film range is claimed to offer a high-performance, ‘seal and peel’ solution for renewable pulp and pressed board trays, to allow manufacturers to respond to widespread consumer demand for new sustainable packaging solutions. Combining a renewable resource tray with KPeel lidding presents manufacturers with an economical first-step in plastic reduction, it said.
UK-based flexible packaging and lidding films supplier, KM Packaging, has developed a new, resource efficient, reduced-plastic packaging for its KPeel range of lidding film solutions. The mono-PET film range is claimed to offer a high-performance, ‘seal and peel’ solution for renewable pulp and pressed board trays, to allow manufacturers to respond to widespread consumer demand for new sustainable packaging solutions. Combining a renewable resource tray with KPeel lidding presents manufacturers with an economical first-step in plastic reduction, it said.
KPeel lidding film range, which is available in thickness of 16-40 microns, is suitable for ambient, chilled, frozen and dual ovenable applications, as well as for printing, perforation and lamination to add functionality such as high barrier or improved strength. Its transparency and clarity also create shelf appeal for fresh produce in pulp punnets, such as tomatoes and strawberries, says the firm. KM Packaging’s compostable range of lidding films is also currently in trial and will present additional opportunities for sustainable packaging solutions.
Packaging supplier Tri-Star Packaging has launched new packaging products made in part from rPET. First in the line-up is the KC range of deli pots, consisting of four round pots made from high-clarity rPET. The new range, according to the British company, is lighter in weight, lowering its carbon footprint. The stackable deli pots are said to give food-to-go retailers even more flexibility and shelf presence with their takeaway offers. The Tri-Green range’s key feature is that it is made from premium rPET.
Meanwhile, early this year, Australia-headquartered packaging giant Amcor said that it was committed to significantly increasing its use of recycled materials, adding that it is “the first global packaging company to commit to working towards 100% recyclable or reusable packaging by 2025”.
Amcor followed up on this by commercialising what it says is its “game-changing” LiquiForm technology with the first consumer packaging. It produced a bottle, which contains 50% PCR content, as a drop-in replacement for the current Nature’s Promise brand of hand soap and uses the existing closure and label. Amcor partnered with Greenblendz, a US-based co-packer and developer of private label consumer products. Amcor produced the 12 oz PET bottle on a proprietary Amcor-built machine powered by the LiquiForm process.
In addition to reducing supply chain costs, LiquiForm technology is touted to improving packaging consistency and lowering the carbon footprint associated with filling and packaging. This is because it uses the packaged product instead of compressed air to simultaneously form and fill containers. In this case, the hand soap essentially forms its own rigid PET container using the LiquiForm process. By combining the forming and filling into one step, the process eliminates costs associated with the equipment and energy of the traditional blow moulding process along with the handling, transport, and warehousing of empty containers.
The forming of bottles with Amcor’s LiquiForm process also opens new pathways toward lighter, more sustainable packaging. Lighter weight containers, achieved through improved consistency in wall thickness, combined with a reduction in the transport of empty containers, reduce environmental emissions and lower the carbon footprint. Plus, the process offers the potential to reconfigure supply chains and move packaging closer to the market, resulting in strong logistical benefits and further carbon footprint reductions, said the firm.
Joining forces to secure supply, market growth
The growth of opportunities for PCR in packaging is backed by the increasing use of rPET as a means of scaling down the use of virgin plastics in packaging. Major industry players are also moving in to drive closed loop solutions for the packaging sector.
Since rPET resin is widely used for food and beverage packaging as well as fibre applications in Europe, according to Thailand-headquartered chemical producer Indorama Ventures (IVL), it is acquiring French plastics recycling facility Sorepla Industrie. It added that the demand for food-grade rPET in Western Europe is expected to grow at a CAGR of 7% from 2018-2021.
Sorepla, one of the largest recyclers in Europe, has three production lines for rPET, recycled high density polyethylene (rHDPE), and food-grade pellets, with a combined capacity of 52,000 tonnes/year.
This acquisition is expected to further solidify IVL’s position as one of the leaders in recycling in Europe and opens up new opportunities to serve increasing demand for food grade rPET. According to IVL, while it can rely on its French subsidiary, Wellman France Recyclage in Verdun, the acquisition of Sorepla gives the company additional capabilities to deliver food-grade rPET to serve increasing demand among major brand owners for more sustainable packaging solutions, especially hinging on Sorepla’s proximity to its existing recycling business and supply chain.
Austrian packaging solutions specialist Alpla Group, and Fromm, a Switzerland-headquartered company producing load securement systems for the transportation of goods, are partnering up in PET recycling to further optimise the already high recycling rates for PET as well as a significant reduction in CO2 emissions through saved transport. Both companies operate recycling plants for PET bottles, thus ensuring the necessary supply of materials for their own production facilities.
The collaboration also further benefits the partners, such as simplified access to markets in the respective countries, as well as ensures the necessary quantity and quality of materials for production for both sides.
The PET recycling team plants in Wöllersdorf (Austria) and Radomsko (Poland) are part of the Alpla Group, and have a capacity of approximately 45,000 tonnes/year of food-grade rPET produced from post-consumer materials.
Meanwhile, PET recycling company Texplast in Wolfen (Germany) has been a subsidiary of Fromm Plastics since 2004. Texplast produces PET pellets and PET flakes. Fromm uses these for its own production of strapping bands and also supplies manufacturers of beverage bottles, thermoforming sheets and fibres.
Packaging is vital to assuring the safety and effectiveness of an extensive range of food, beverage, medical, pharmaceutical, household and personal-care products. It also significantly limits the enormous environmental implications from food and other product waste. All in all, it can be seen that the brand majors in the packaging sector are working towards this effort of sustainability.
Chinese economy to grow over 6.5 pct in 2018, 2019: report
BEIJING, March 1 (Xinhua) — China’s economy will grow by over 6.5 percent this…