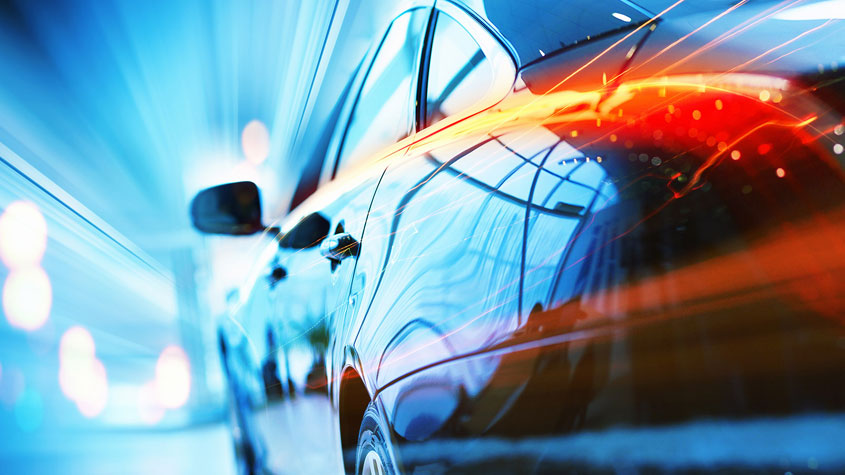
By 2025, plastics will account for 25% of an average car, industry analyst IHS Chemical claims in a study.
Currently, the automotive industry uses about 700,000 tonnes of plastics in cars, up by 29% or 900,000 tonnes by 2020 as car makers bank on design innovations to spur cost savings and fuel efficiency. But with sustainability being a big part of the automotive industry, car majors are turning to the use of post-consumer recycled (PCR) material in car components, says Angelica Buan in this report.
Green message in a bottle
Discarded PET bottles are usually recycled to make new bottles. But for Easicomp, a German producer of long glass fibre-reinforced thermoplastics and a main adversary of the UpcyclePET project, recycled PET (rPET) from bottles can be used in the production of other high-grade industrial applications such as car parts. The process, however, is more of upcycling than recycling, Dr Tapio Harmia, CEO of Easicomp, stressed.
With upcycling, lightweight components are created out of fibre-reinforced rPET, and thus reduce the use of glass fibre-reinforced polyamides typically applied in the production of automotive parts, such as engine mounts or cross members. The project, which also ropes in Fraunhofer Institute for Structural Durability and System Reliability LBF and Öko-Institut, involves using a pultrusion process to reinforce the rPET with long glass fibres, and to combine the latter’s mechanical advantages with the special properties of PET, such as lower swelling capacity and good dimensional stability.
Upcyling of PET waste is an environmentally viable solution for creating durable products as it aids in replacing plastics with much higher greenhouse gas emissions, Dr Andreas R. Köhler from Öko-Institut said.
American car maker General Motors (GM), which manufactures Buick, Cadillac, GMC andChevrolet luxury car brands, has been a pioneer in using post-consumer materials. It has used rPET from bottles to produce noisereducing fabric insulation for the Chevrolet Equinox engine.
GM’s Zero Waste agenda includes expansion of its landfillfree programme as all of the company’s manufacturing plants in Canada, Mexico and South America recycle, reuse or convert to energy waste from daily operations. GM says it has 142 manufacturing and non-manufacturing landfill-free facilities globally to keep resources in the value chain and reduce greenhouse gas emissions.
Rolling out cars with more recycled content
Swedish luxury car Volvo will start using 25% recycled plastics in every newly launched car from 2025. The car maker, acquired in 2010 by Chinese firm Zhejiang Geely Holding Groupfrom Ford Motor, is pushing its antipollution plan by using recycled plastics from fishing nets or PET bottles in car dashboards or carpets, it said.
Last year, Volvo sold more than 500,000 cars that had around 5% of recycled plastics content. To demonstrate the viability of this plan, Volvo has made an identical version of the XC60 T8 plug-in hybrid SUV but with plastic components replaced with equivalents containing recycled materials.
The specially-built version of the XC60’s interior has a tunnel console made from renewable fibres and plastics from discarded fishing nets and maritime ropes. The floor carpet contains fibres made from rPET and a recycled cotton mix from clothing manufacturers’ offcuts. The seats also use PET fibres from plastic bottles. Used car seats from old Volvo cars were used to create the sound-absorbing material under the car bonnet.
Volvo, which aims to have climate neutral manufacturing operations by 2025, has also committed to eradicate single-use plastics across all its premises and events by the end of 2019, not to mention that it is also electrifying all new cars launched after 2019.
Meanwhile, Austrian plastics maker Borealis, which is supplying Volvo with PCR material for its cars, is launching new investments to increase its share of recycled plastics in major applications such as vehicles. Recently, it acquired Austrian plastics recycling company Ecoplast Kunststoffrecycling, to tap into the growing recycled polyolefins (PO) demand. Ecoplast processes 35,000 tonnes/year of household and industrial plastic waste, turning it into quality LDPE and HDPE recyclates for the plastic film market and for other applications.
Borealis says it has made PO recycling a key element of its overall PO strategy because of its potential to support both growth and sustainability. The company has been a stalwart in making PO more circular. In 2014, it began offering high-end compound solutions to the automotive industry, consisting of 25% and 50% PCR content.
Borealis claims it was also the first virgin PO producer to explore the possibilities of mechanical recycling, by acquiring German post-consumer PO recyclers mtm plastics and mtm compact in 2016. Borealis invested EUR15 million into mtm plastics, which is expected to bring the overall input processing capacity from 60 kilotonnes to 80 kilotonnes. Besides the capacity increase, the investment aims at improving the capability to address the needs of the high-end market of re-granulates, Borealis furthered.
Heavy impact of reinforced polymers in lighter vehicles
A typical car has more than 1,200 kg weight of various materials, including about 110 kg of plastics and six times more steel and about 70 kg of iron, and about half as much aluminium and rubber. With this composition, it is difficult to imagine how cars can be produced lighter.
Integration of carbon fibre-reinforced plastics in the manufacture of vehicle parts has been attested to reduce vehicle weight by as much as 50%.
As cited in a Mordor Intelligence market report, increasing applications in the automotive industry is a major driver for the growing carbon fibre market that is anticipated to reach US$6 billion by 2023.
Automotive makers including BMW, Mercedes-Benz, McLaren, Chevrolet, Lambhorgini and others, are increasing the use of carbon fibre to replace metals in their vehicles, and thereby reduce the weight of vehicles.
In terms of sustainability, Tokyo-basedMitsubishi Chemical is venturing into recycling carbon fibres for the production of car parts, through its subsidiary Shinryo. Mitsubishi has already installed equipment at its Kurosaki plant in Fukuoka Prefecture. The plant has the capacity to recover as much as 100 tonnes/year of carbon fibre through the vaporisation process. Thereafter, Mitsubishi plans to increase the scale of the recycling process as operations are established.
Meanwhile, Borealis, together with its Abu-Dhabi National Oil Company-joint venture company Borouge, has introduced Daploy carbon fibre-based polypropylene (CFPP), made from reclaimed carbon fibre material.
According to the partners, Daploy WB140HMS has been used by a Japanese plastics processor in the foamed blow moulding process to produce automotive air ducts, resulting in part weight savings of up to 80%, which in turn leads to overall improved fuel efficiency and lower CO2 emissions.
The recently launched CFPP product Fibremod CF061SY, on the other hand, has been used by a North American OEM to make the A-pillar brackets on a top-selling commercial vehicle. It has also been used by US car part maker Magna Exteriors to produce a class-A fender.
Having modified an existing tool capable of producing a viable thermoplastic alternative to a conventional metalstamped part, Magna Exteriors selected a Borealis Fibremod carbon development grade containing 10% carbon fibre-reinforced PP. This enabled the manufacturer to achieve both the exterior part impact performance required for crash and pedestrian safety, and the high-quality look of a class-A painted part, it said.
Yet, because the part is made of reclaimed carbon fibre, the body panel weighs 30%-40% less than conventional aluminium panels, and enables zero gap performance with low CLTE when compared to other engineering plastics.
This makes the exterior application more recyclable, of a lighter weight, and thus more sustainable.
Unlike polyamides (PAs), CFPP is not hygroscopic, meaning it does not absorb moisture. Compared to other plastics, CFPP products help minimise ‘squeak and rattle’ noises, Borealis intoned.
Meanwhile, the companies have also invested in new production facilities, including compounding plants in China and the US, to secure the growing demand for PP on account of developing anglobal market for electrification and self-driving vehicles.
Borealis’s North Carolina compounding plant, which will produce up to 30 kilotonnes/year of its proprietory PP compounds for the automotive industry, is expected to start commercial production in 2019. Borouge expects to start commercial production at its expanded polymer compounding plant in China by late 2020, while its 480,000- tonne/year PP unit (PP5 Project) at Ruwais in Abu Dhabi is set to be completed by 2021.
Circular car in the making
Elsewhere, to showcase the closed loop chain and how far biobased materials have come, the world’s first biobased, circular car has been successfully designed and built in the Netherlands by the Technical University of Eindhoven. This is the first time that a car chassis and all bodywork have been made from natural and biobased materials, with no metal or traditional plastics used for the structural parts of the car. The parts are made of light and strong sandwich panels, based on natural fibre flax and Luminy polylactic acid (PLA) resin supplied by Total Corbion PLA.
Dubbed Noah by the TU/ecomotive student team, the car was designed for city use and features two seats and a spacious trunk. In addition to its biobased composition, it is also ultra-light and electrically-powered. Noah reaches a top speed of 110 km/hour and the battery range lasts up to 240 km. At 360 kg, the weight of the car excluding batteries is less than half the weight of comparable production cars. In addition to being biobased, the parts are also recyclable, resulting in a 100% circular car, sustainable in all life phases, said Total, adding that the car is doing a European tour to showcase its features.
Thus, over the next decade, the automotive industry will double up the circularity of plastics; and manufacturers who are committed to sustainability in their manufacturing ethos are expected to scale up post-consumer/biobased plastic content in the cars they are producing.
Chinese economy to grow over 6.5 pct in 2018, 2019: report
BEIJING, March 1 (Xinhua) — China’s economy will grow by over 6.5 percent this…