3D Printing/Additive Manufacturing: 3D printing gains traction
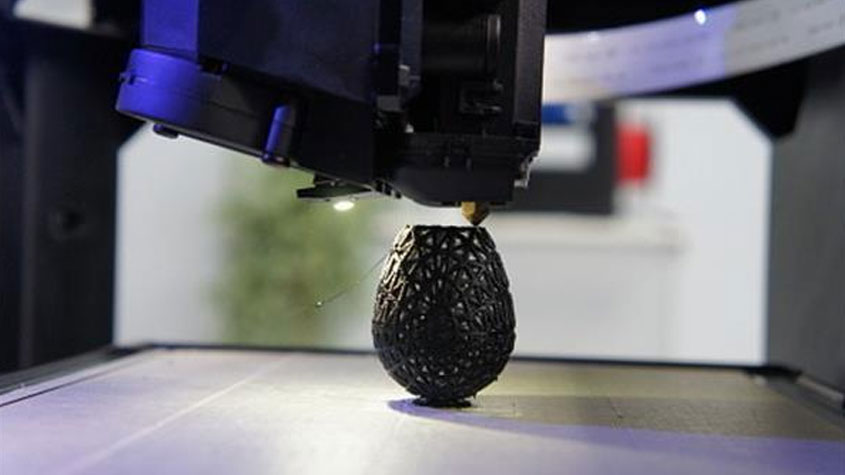
Additive manufacturing (AM), or 3D printing as it’s better known as, is emerging as an alternative processing method since it offers designers more latitude than conventional manufacturing methods.
Its emergence was noticeable at the recently concluded K2016 show held in Düsseldorf, Germany, from 19-26 October, and while the automotive and aerospace industries are currently the main sectors, 3D’s reach is being extended to other sectors.
3D market growth and advantages
AM processes can improve productivity by quickly converting digital designs into functional parts for low to medium volume production without the time or cost required to first build a moulding tool and prototype. Thus, they can significantly accelerate the time-tomarket for OEMs and Tier suppliers.
AM also significantly reduces production waste, optimises the supply chain, eliminates tooling and speeds the time to market for new designs requiring the same high performance expected from traditional polymer conversion methods. In contrast, however, it lends itself to a revolutionary democratisation of manufacturing through digitisation and file, rather than part transfer.
According to a research report by Markets and Markets, the 3D printing market is expected to reach US$30 billion by 2022, growing at a CAGR of 28% between 2016 and 2022. The US is expected to be the largest growth market and the speed at which it has taken up 3D printing has been astounding, with 71% of US manufacturing companies now using 3D printing in some way, with 31% adopting it for rapid prototyping, says a study by consulting company PwC. The study showed that 42% of manufacturers expect to use 3D printing for mass manufacturing in the next 3-5 years, but just 6% are using it to produce end products right now.
Materials makers advance research
Since key patents on 3D printing processes expired around two years ago, manufacturers of traditional printers and large chemical companies have also entered the 3D business.
Materials maker Solvay showcased a 3D-printed functional air intake manifold designed for the Polimotor 2 racing car project. It uses the company’s Sinterline Technyl 40% fibre-reinforced PA6 powder and is produced by selective laser sintering (SLS). Solvay says it was able to produce the part with a 30% weight reduction by applying its predictive simulation package, MMI Technyl Design, to a functional 3D printed part for the first time. The Polimotor 2 project aims to develop an engine weighing 40 kg less than today’s standard production engine.
Also, Solvay showcased the throttle body of the air intake manifold, which was produced with a 10% glass-filled KetaSpire PEEK polymer filament using Fused Filament Fabrication (FFF), also known as Fused Deposition Modelling (FDM).
The company already has an AM technical centre/ facility for Sinterline Technyl in Lyon, France, and recently opened a new laboratory at its R&D centre in the US and a facility in Brussels, Belgium, dedicated to AM software design, powered by Digimat from e-Xstream, an MSC Software company.
Another chemicals company jumping on the 3D bandwagon is Germany-based BASF,teaming up with printer maker HP, to offer new 3D printing materials through the HP Multi Jet Fusion Open Platform, which allows customers to select a material supplier, such as BASF, and engage with them directly to develop materials for specific 3D applications. BASF and HP are now collaborating to develop materials for large-scale production.
BASF says that in the chemical industry, it has the broadest portfolio of materials that can be developed for 3D printing, such as engineering thermoplastics, polyurethanes, acrylate systems (eg. photo-polymers), photoinitiators,functional additives, stabilisers and pigments as well as metal systems. It recently launched Ultrasint PA6 X028, a PA6 powder for SLS. To coordinate its latest development, BASF has established a new 3D business unit and created an Application Technology Centre for 3D printing in Heidelberg, Germany.
HP’s Multi Jet Fusion technology is similar to 2D printing, where a print-head applies agents in the envisioned shape on a polymer powder, but differs from SLS, where powder is applied and then melted bit by bit with a moving laser. BASF claims that compared to other 3D printing technologies, HP’s Multi Jet halves the costs. Car maker BMW and mega sporting shoe supplier Nike have adopted HP’s new printing technology.
In Asia, Chinese automotive materials compounder Xinda Group is creating a network of solution providers across the AM value chain from universities to equipment manufacturers. It has been given a hefty sum of RMB45 million from China’s Ministry of Science, over four years, to pioneer research in the 3D sector.
“Xinda will lead the project and will conduct research in processing equipment and materials,” said Charles Wang, Managing Director, speaking to PRA at K2016. “We will also collaborate with industry institutes as well as the University of China Academy of Science and participants from many industries,” Wang added, explaining that the research is targeted at processing equipment/materials for applications in aerospace and electronics.
Xinda will also set up a global R&D centre based in Shanghai, which will be opened in 2017. The firm started global production four years ago when it built a manufacturing site in Dubai to better serve its international customers in Russia and Middle East.
Meanwhile, a new development collaboration between Airbus Group Innovations, LSS Laser Sinter Service and Lehmann & Voss has been launched to bring ThermoMelt, a new 3D printing process developed by Airbus. It is said to reduce the cost of producing high performance polymers, like PPS and PAEK, by lowering required sintering temperatures. German service bureau Rauch CNC will also join this collaboration as a partner for testing ThermoMelt and to ensure it fulfills market requirements.
ThermoMelt allows the production of parts using high performance materials in slightly modified commercial SLS machines that are already in the market. These modifications will provide better thermal and laser control to the system. Furthermore, ThermoMelt also significantly reduces the thermal ageing effects during the manufacturing process, increasing recyclability and reducing costs compared to standard additive layer manufacturing techniques. The collaboration is expected to commercialise the ThermoMelt process.
COC for prototyping medical parts/devices on 3D printer
US-based microfluidics equipment supplier Dolomite unveiled its Fluidic Factory, the first commercially available 3D printer for sealed microfluidic devices, which utilises cyclic olefin copolymer (COC) from Topas Advanced Polymers.
COC was selected due to its ultra-high purity, lower leachables and extractables than competing materials, making it ideal for microfluidics in biology and medical environments, according to Dolomite. The inert nature of the standard moulding grade Topas 8007S-04 also prevents interference with reactions and analyses. Other features include UV transparency and low autofluorescence.
The firm says its compact 3D printer, ideal for benchtop or desktop use, features intelligent software and hardware for sealing of fluidic paths, allowing the creation of precise channel geometries and various features not possible using etching, embossing, moulding, or machining techniques.
Users can choose a design from the selection in the Fluidic Factory’s Design Library, or create and print their own device using virtually any CAD software. It enables rapid prototyping of fluidically-sealed devices such as chips, sensor cartridges, fluid manifolds, valves, connectors, and medical devices, including organ-on-a-chip, point-of-care diagnostics, drug development, education, chemical synthesis, and analytical and biomedical assays. Manufacturers can also ramp up to commercial-scale moulding without changing plastic materials.
3D printing filaments expanded
While 3D printing has been one of the most rapidly growing industries over recent years, only limited thermoplastics materials, such as PLA, ABS and PA11, have been available to be used for the process.
Many companies have been trying to bridge the gap between end users’ expectations and the materials available in the market by introducing new products.
One of these is Spanish ABS speciality compounderElix Polymers that has been working in collaboration with AIMPLAS Plastics Technology Centre in Valencia to develop advanced versions of its terpolymer for 3D printing using FFF. Its aim is to produce parts with better mechanical properties, such as good impact resistance, low warpage, strong dimensional stability and high resolution. It says early functional parts target healthcare, appliances, automotive, and electronics industries.
Dutch chemicals firm DSM is partnering chemical/ plastics distributor Nexeo Solutions to bring new performance filaments for FFF/FDM technology. Its Arnitel ID thermoplastic copolyester is said to reach elongation at break up to 400% and exhibits better layer-to-layer adhesion compared with available ABS, PLA and TPU filaments used in 3D printing. Anothergrade, Novamid ID, is a PA originally developed as speciality product line for the automotive and electronics industries that can withstand harsh environments and high temperatures of up to 150°C. The high crystallinity of the polymer allows for designs with overhangs. DSM now offers the materials as filaments, instead of plastic granules.
Meanwhile, South Korea’s SK Chemicals has launched Skyplete thermoplastic material solutions for 3D printing utilising its own proprietary resins, such as PLA, and compounding technology. It says that its materials do not contain hazardous components such as styrene or BPA, which can be found in ABS or PC. There are five product series: E, G, T and L products for filaments used in FFF/FDM, and S power products of PPS, PLA, PCT and TPEE, to be used for powder bed fusion such as SLS.
Space is the new frontier for 3D printing
Brazilian materials maker Braskem partnered US-based developer of zero gravity 3D printers, and an official supplier to NASA, Made In Space, to utilise its bio-PE for 3D printing of spare parts and tools in space.
The first part was a pipe connector for a vegetable irrigation system, which was fabricated by the Additive Manufacturing Facility (AMF), the first commercial 3D printer permanently allocated in space. The equipment, which will fabricate various types of parts using Braskem’s sugar cane-based green plastic, is located on the International Space Station (ISS) and was developed by Made In Space with the support of the Centre for the Advancement of Science in Space (CASIS).
The companies say astronauts will be able to receive by e-mail digital designs of parts and then print them, which means time and cost savings.
The bio-PE was chosen because of its flexibility, chemical resistance and recyclability since it is made from a renewable resource, says Braskem.
Meanwhile, the printing bed of the 3D printer is also made of Braskem’s Utec ultra-high molecular weight polyethylene (UHMW-PE).
Printer for silicone parts first in industry
German chemicals company Wacker Chemie launched its Aceo Imagine Series K printer for silicone rubber parts, since the company says up till now “there is no mature 3D printing technology available for silicones”.
The 3D printing device is based on a dropon demand method developed by Wacker. The printer head deposits tiny silicone droplets on a substrate, building a part layer by layer. The silicone is formulated so that the droplets flow together before the UV-light activated curing process begins to produce a homogeneous part not much different from injection-moulded parts. With the aid of water-soluble support materials, it is also possible to create overhang materials and internal lattices.
The firm says 3D printing is growing rapidly in medical applications, especially in biomodelling, as well as customised geometries. Silicones are suitable for these types of applications due to properties of heat resistance, flexiblility at low temperatures, transparency and biocompatibility. They can furthermore be pigmented in any colours and have good damping properties.
Starting August, Wacker has been offering Aceo services with customers able to upload their own designs in a webshop and order 3D-printed silicone parts. These will be produced in the Aceo print fab. Wacker says it is also currently building its own Aceo technology centre near its main site in Burghausen, Germany. In the future, customers will be able to test their own product ideas in the laboratory.
Arburg steps up technology with Freeformers
German machine maker Arburg was one of the first to stir up interest in 3D printing, when it premiered a prototype Freeformer at the previous K show in 2013.
Arburg, stating that it is satisfied with the worldwide response to its Freeformer, with some customers already purchasing further Freeformers after less than one year, has since K2013 stepped up its technology known as Arburg Plastics Freeforming (APF). It had three exhibits at K2016, with the first combining 3D printing, injection moulding and Industry 4.0. As part of an IT-integrated spatially distributed production set-up, the Freeformer was individualising “smart” luggage tags in batches of a single unit and using TPE plastic to apply a 3D graphic previously selected by a visitor to the booth.
Another Freeformer used the example of a toggle model (scale 1:16) to show how APF can be used to produce complex functional parts, over a period of around 200 hours, in other words over the course of the entire trade fair! The part was produced from ABS. The second discharge unit applied supported material to implement the necessary complex geometries. Consisting of around 100 million drops, the resulting “block” fills almost the entire build chamber, which is designed to accommodate a maximum of 154 x 134 x 230 mm parts. After the support structure was dissolved in the warm water tank, the 738 g-toggle was revealed, with around 30 moving joints just like the toggle of a moulding machine.
On the third Freeformer, Arburg was processing a high-temperature material, Sabic’s polyetherimide (PEI) Ultem 9085, to produce spacers used in Allrounder machines, weighing just 0.09 g, in small batches. The build time for 70 units is around three hours. The firm says the PEI parts display good mechanical properties and are suitable for high continuous working temperatures. They have a very high specific strength and rigidity and dielectric strength, as well as UV and gamma radiation resistance. The material is therefore also suitable for applications in the automotive and aerospace industries.
Chinese economy to grow over 6.5 pct in 2018, 2019: report
BEIJING, March 1 (Xinhua) — China’s economy will grow by over 6.5 percent this…