3D Printing/Additive Manufacturing: Strokes of innovation in medical technology
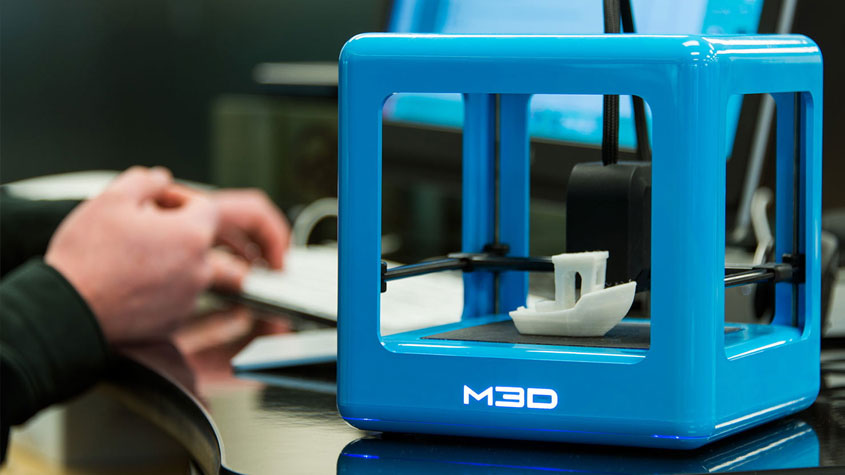
The application of 3D printing in medicine and healthcare is transforming patient care and improving outcomes, says Angelica Buan in this article.
The demand to increase patient recovery and decrease downtime is pressing medical device manufacturers to craft cost-effective, innovative products. Customisation of medical devices through 3D printing technology is one way of ensuring that individual needs are met. Its application in medical devices also enables better surgical planning for safer medical procedures.
3D printing is witnessing wider adoption in the medical devices sector, with the former projected to exceed US$2.3 billion by 2024, according to Zion Market Research.
3D printing technology helps in hip and jaw replacements, the creation of limb prosthetics and plastic tracheal splints, and other implantable devices. As well, it abets in the development of prototypes to be used by doctors when planning for surgeries to reduce errors.
A 3D object formed from a digital 3D file is a computer-aided design drawing or a magnetic resonance image (MRI). In this process, a 3D object is created by constructing consecutive layers of material. Each layer is attached to the prior layer until the object is completed.
Given its huge potential, 3D printing technology, also called additive manufacturing, has continued to advance from its stereolithography progenitor; and from its beginning applications as dental implants and custom prosthetics.
More effective drug delivery
Cancer is the second leading cause of death globally, and is responsible for an estimated 9.6 million deaths in 2018, according to the World Health Organisation (WHO). However, advancements in medical care and technologies are helping reduce the mortality rate from the disease.
A new 3D-printed implant has been developed by the Southwest Research Institute (SwRI)and the University of Texas at San Antonio (UTSA). The said implant, when injected in a patient’s body, could deliver a personalised dose of medicine to treat infections as well as ailments such as arthritis, cancer and AIDS. The project, led by Albert Zwiener of SwRI’s Chemistry and Chemical Engineering Division and Dr. Lyle Hood of UTSA’s College of Engineering, is supported by a US$125,000 grant from the Connecting through Research Partnerships (Connect) programme.
The design incorporates complex geometries to personalise each device to an individual’s ailment and takes advantage of the selective timing and release of the compound. The team will create the device with a specialised 3D printer at UTSA that can print biodegradable materials. This makes removal of the implant unnecessary, as it will simply dissolve inside the body when the treatment is complete.
The implant is also engineered to trigger localised immunotherapy for cancer treatments. Immunotherapy enlists the body to attack cancerous tumours. The SwRIUTSA team believes that the device’s localised treatment capabilities can trigger the body to destroy the invasive cancer.
For a drug to be effective, patients must take a minimum amount, but not so much that it makes them ill or causes serious harm. As a result of those limitations, someone who needs frequent doses of a specific medicine either has to take a pill each day or visit a doctor for treatment. To remedy this, the SwRI-UTSA team is working to create an implantable device that can deliver a controlled, personalised dose of medicine over several weeks.
While the implant is ideal for cancer treatment, it’s designed to work with any type of drug and could have a significant impact on a wide array of diseases and ailments.
New developments, synergies in spinal solutions
Engineers and medical researchers at the University of Minnesota have created a 3D printed device that could help patients with long-term spinal cord injuries regain some function.
Made of silicone, the 3D-printed guide serves as a platform for specialised cells that are then 3D-printed on top of it. The guide will be surgically implanted into the injured area of the spinal cord where it would serve as a type of “bridge” between living nerve cells above and below the area of injury. The hope is that this would help patients alleviate pain as well as regain some functions like control of muscles, bowel and bladder.
Meanwhile, in bid to develop improved spinal treatment solutions, Johnson & Johnson Medical Devices Companies, through its subsidiary Johnson & Johnson Medical GmbH, acquired Emerging Implant Technologies GmbH (EIT), a privately held German manufacturer of 3D-printed titanium interbody implants for spinal fusion surgery. The products in this portfolio leverage EIT’s proprietary advanced cellular titanium, which consists of an open and interconnected porous structure designed to allow bone to grow into the implant.
This acquisition allows DePuy Synthes, the orthopaedics business of Johnson & Johnson, to enhance its comprehensive interbody implant portfolio that includes expandable interbody devices, titanium integrated PEEK technology and now 3D-printed cellular titanium, for both minimally invasive and open spinal surgery.
The EIT technology complements DePuy Synthes’s investment in the interbody implant segment in spine, including the recent introductions of the Concorde Lift Expandable Interbody Device, and in the US, the Proti 360 family of titanium-integrated Interbody Implants, designed to treat patients with degenerative disc disease.
Potential in implants to do away with amputations
Amputations can be prevented with 3D printing technology. This is a positive development that has transpired from a study published in the Foot & Ankle International (FAI) journal. It said that 3D printing has allowed foot and ankle orthopaedic surgeons to use custom-made implants for difficult foot and ankle cases. It is found that implants offer a new approach to treat complex lower extremity pain and deformities, while employing the benefits of unlimited shapes, increased options in size, and less morbidity or complications.
Researchers at the Duke University Department of Orthopaedic Surgery studied 15 patients who received custom 3D-printed titanium implants between 2014 and 2016 to treat poor bone quality, bone loss, and deformity. In each case, the implants were initially developed by obtaining a computed tomography (CT) scan of the patient and uploading the data to a software programme that allowed 3D manipulation of the bones and joints. From there, the senior surgeon and company engineers designed and approved the implant.
The team spoke of the study as the “first to demonstrate improvement in patient-reported outcomes with the use of 3D-printed implants”. They said that injuries of many of the patients treated in this study would have required an amputation without this technology.
The authors of the study suggested that 3D printing could revolutionise medical care, specifically in modelling for medical education and creating custom artificial body parts. The study notes that longer-term followup is needed to understand the longevity and potential complications of these 3D-printed implants.
Along the same track, Georgia Institute of Technology engineers have developed custom-made splints using 3D printing technology, which were recently used for a paediatric patient.
The seven-month old patient had congenital heart disease and tracheo-bronchomalacia, a life-threatening condition characterised by airway obstruction. The clinical team surgically inserted an experimental 3D-printed tracheal splint (that will be absorbed by the body) to open the patient’s airways and expand his trachea and bronchus.
The splints were created using reconstructions of the patient’s airways from CT scans. Although the novel device has proven its potential, it is still under development. Its safety and effectiveness have yet to be determined, thus it is not available for clinical use. For the aforementioned case, the medical team sought emergency clearance from the US FDA to carry out the procedure under expanded access guidelines.
Bioprinted parts
At one point in the medical history, the concept of lab-produced human body parts has raised heavy ethical concerns. Nevertheless, bioprinting body parts has gained acceptance as a cost-effective solution to preserving the quality of life in cases of impairment.
The global 3D bioprinting market is projected to reach US$2.6 billion by 2024, according to Grand View Research. 3D bioprinting is used for printing medical instruments, prosthetics, and dental and bone implants, as well as in pharmaceutical manufacturing.
Among the leading players in bioprinting is Aether, an American technology start-up and maker of Aether 1, the world’s most advanced 3D bioprinter. Aether’s recent undertaking is its collaboration with researchers from UCLA Henry Samueli School of Engineering to improve the fabrication process for 3D printing artificial muscles with soft materials.
Aether will develop new techniques and algorithms to optimise Aether 1 and its computer vision features in order to automate the process of 3D printing soft robotic devices, improve print quality and ease of use.
The collaboration will focus on developing technologies for faster, easier, high-quality fabrication of soft artificial muscles and complex multi-material structures. A freshly completed major upgrade to Aether 1’s automatic offset calibration system makes embedding conductive materials easier than before.
The system uses computer vision to automatically calculate precise offsets for multiple tools and tool types, enabling users to extrude multiple materials side by side without overlapping or gaps. Conductive materials like graphene or silver nanoparticles can now be easily printed directly into robotic devices, replacing traditional wires.
Thus, it can be seen that the 3D technology is growing rapidly, for prototyping, industrial and medical uses.
Chinese economy to grow over 6.5 pct in 2018, 2019: report
BEIJING, March 1 (Xinhua) — China’s economy will grow by over 6.5 percent this…