Finding a middle ground for pollution and resource security
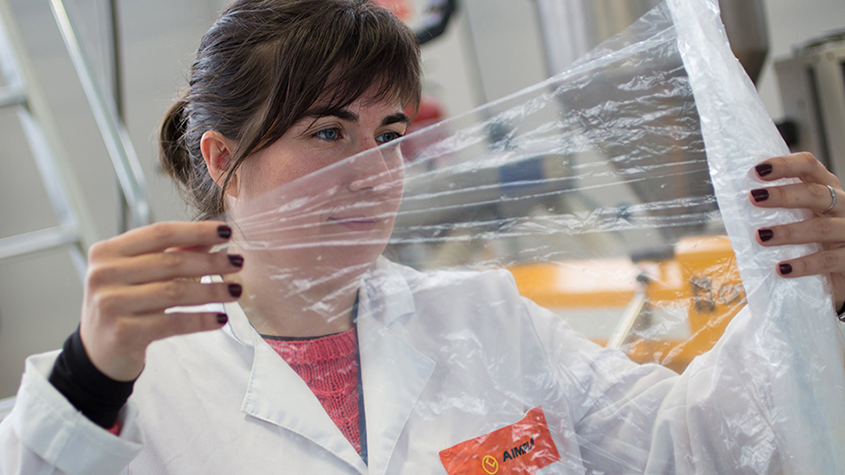
Bioplastics developments are attempting to solve the waste plastics overgrowth without causing further harm to the environment, says Angelica Buan in this article.
The plastic waste pollution is an issue that seems to refuse to die. The amount of plastics that is generated globally runs at 300 mega-tonnes/year. At this rate, some experts claim that our use of plastics, a ubiquitous material in the modern world, has become incessant and that it is accelerating the world’s journey towards Anthropocene.
The industry, however, has remained optimistic that is not quite the case. In fact, initiatives are being rolled out to heighten awareness to waste segregation, recycling, and reuse. To top it all, the circularity model is being integrated across various industries to recover waste plastics and to turn them into high value products.
Biobased plastics or bioplastics, derived from renewable feedstocks such as corn, sugarcane, and cellulose, are making inroads in various applications in end-user industries that favour plastics, including rigid and flexible packaging, agriculture, consumer goods, automotive, electronic, building & construction, and others.
While development of bioplastics has certainly gone a long way from its 19th century cellulose-based Parkesine and casein-based antecessors, adoption has been hampered by high production costs and limited performance compared to traditional plastics.
Furthermore, feedstock used for bioplastic has raised the concern about food security, land conversion, and usage of water. Is bioplastics production taking away resources that are already scarce? It is unlikely, especially since food wastes that are unrecovered and landfilled are developed as bases for producing bioplastics.
Rooting for agro waste-turned-plastics
Renewable feedstock also comes from food wastes. Approximately a third of all food produced globally is lost in the supply chain between the producer and the market; or goes to waste, as a result of spoilage or discarding of edible food parts, according to the UN Food and Agriculture Organisation (FAO).
Technology plays an important role in lessening food wastage by turning it into feedstock for bioplastics. Thus, collaborations among industry stakeholders and academic experts are on the rise to develop technologies.
Orange peel waste is being put to good use as durable and biodegradable plastic material through the MIPLASCOE project, formed by Spanish companies including wine maker J. Garcia Carrion; Agrocode Bioscience; industrial laboratory Canagrosa and plastic packaging and recycling firm Plastipak. It also involves plastic extrusion company Lisanplast; construction group AZVI; as well as research organisations, namely, AIMPLAS, Polytechnic University of Valencia (UPV), and the University of Sevilla.
Orange peels are common agricultural wastes in Spain, the country being Europe’s top orange producer, accounting for over half the region’s total production, according to EUROSTAT.
MIPLASCOE aims to produce biopolyesters, by means of fermentation from the waste of Spain’s orange juice industry, for the transportation and bottle packaging sectors.
According to Dr Pilar Villanueva of AIMPLAS, the fruit sector has generated considerable volumes of wastage that is coursed to the manufacturing of pellets for animal feed or is landfilled. The first solution is costly from the energy point of view on an industrial scale and in both cases problems arise for the environment.
Thus, the consortium has been working on the synthesis of polybutylene succinate (PBS) from succinic acid and butanodiol, by polycondensation, achieving at laboratory scale a molecular weight (MW) from 15.000- 50.000.
The development of MIPLASCOE, from July 2016 to December 2018, is framed within the policies of the European Union (EU) for circular economy and environmental sustainability via green technologies.
From this also the Citruspack project was launched in 2017 at the Aitiip Technology Centre headquarters in Zaragoza, Spain. It aims to turn citrus side-streams into natural additives for the reinforcement of 100% biodegradable plastic bottles and containers.
Besides Aitiip, Citruspack is comprised of Slovenian tool makers association Tecos; Spanish fruit producer AMC Innova; French plastic cluster Plastipolis; Belgian biogas supplier OWS; and Spanish retail chain Eroski.
Meanwhile, the Valencia-headquar tered AIMPLAS has also collaborated with companies Alhóndiga La Unión, Torres Morente, Domca, Neo, Ecoplas y Morera y Vallejo, as well as three other research centres Tecnalia, Cidaf, and Las Palmillas Fundación Cajamar for the BIOVEGE project. Launched in 2016, the project draws on fruit and vegetable waste, such as cantaloupe, watermelon, cucumber, zucchini or peppers, to produce bioplastics with new properties for sustainable packaging as well as bioactive compounds and food preservatives.
The sugars f rom watermelon and melon, for example, are utilised to produce 23 micron-thick biodegradable films to be used as shrink film for packaging. As well, bioplastics ingredients are being extracted from cucumber, zucchini, and other likely by-products.
Last year, the project was awarded for its innovation of new biodegradable mesh nets for green beans by means of reactive extrusion from a combination of biopolymers and additives, with the same properties as conventional PE nets.
Plenty more resources in the sea
Biodegradable bioplastics had been hailed as an antidote to stave off marine litter that is until the United Nations Environmental Protection (UNEP) repor ted that biodegradable plast ics ar e currently “not a solution to marine litter”. It reasons that “plastics, which biodegrade on land under favourable conditions, also biodegrade in the marine environment”, as well, there are no clear standards for biodegradation in the marine environment.
Nevertheless, for lack of other viable options to immediately address marine litter bioplastics are making the case to mitigate this environmental fluke.
New developments utilising compounds obtained f rom crustaceans, algae, and sea organisms ar e making headlines. Too, recent breakthroughs are improving the processes of obtaining biopolymers from these sea species, with the least to zero impact to the environment.
One such new development hones on proteins from squid as the vital ingredient for a bioplastic. The protein found in the squid’s ringed teeth (SRT), can be processed into fibres and films for varied fields of applications ranging from biomedicine and energy to security and defence, according to researchers from Penn State University.
SRT-based materials exhibit elasticity, flexibility and strength, as well as self-healing, optical, and thermal and electrical conducting properties, according to the researchers. For textiles, a source of microplastics in the oceans, SRT protein provides an abrasion-resistant coating that reduces microfibre erosion in washing machines. The self-healing property of SRT protein coating enables longevity and safety of biochemical implants and protective garments; while SRT-based flexible photonic devices used for LED displays, and the like, are also in development.
The SRT proteins are produced without catching a squid, but by using genetically modified bacteria. The process is based on fermentation and uses sugar, water, and oxygen to produce biopolymers.
Elsewhere, Israeli researchers at the University of Tel Aviv are working on algae and ocean microbes for producing biocompatible and degradable plastics. The study, led by Dr Alexander Golberg and Professor Michael Gozin, was recently published in the Bioresource Technologyjournal.
Without requiring land or fresh water, the polyhydroxyalkanoate (PHA) biopolymer is derived from microorganisms that feed on multicellular seaweed and that completely recycles into organic waste.
Goldberg said that plant -based plast ic is not novel, because already these are being produced in commercial quantities. But the bioplastic spin-offs offer much more, he said, as it does not require agricultural land and fresh water as typical bioplastic production does.
“The process we propose will enable countries with a shortage of fresh water, such as Israel, China and India, to switch from petroleum-derived plastics to biodegradable plastics,” he adds.
Optimistic with the outcome of the study, the team has further research in tow to find the most suitable bacteria and algae that would produce bioplastics with different properties.
In the meantime, the Shellworksinitiative, pioneered by design students from The Royal College of Art and Imperial College, has developed new machines to manufacture bioplastic alternatives to single-use plastics. The bioplastic, derived from chitin that is found in the exoskeletons of crustaceans and insects, is versatile and can be adjusted in thickness, transparency, flexibility and stiffness to create a variety of biodegradable objects, they said.
The team built a custom small-scale extractor as well as three custom manufacturing machines: the Dippy, a heated dip moulder to create 3D forms; the Vaccy, a steam-heated vacuum former for making moulded packaging; and the Sheety, a sheet-forming machine for creating controlled flat sheets.
Chitin from crab shells and cellulose from tree fibres are also being harnessed by researchers at Georgia Institute of Technology to create a film as a substitute for flexible packaging.
The new material is made by spraying multiple layers of chitin from crab shells and cellulose from trees to form a flexible film. The resulting film, when fully dried, is found to be flexible, strong, transparent and compostable.
The team compared the material with petroleumbased PET and said that the new material showed up to a 67% reduction in oxygen permeability over some forms of PET, which means, in theory, it could keep food fresher longer.
Showing promise for sustainable packaging, the material is yet to be cost competitive with flexible packaging film, and it needs a manufacturing process that maximises economies of scale. In other words, more research is needed to improve the material’s ability to block water vapour, one of the challenges chitin technology, currently at its infancy, has to overcome.
As it can be seen, scores of bioplastics advancements are emerging, and further R&D is required to be initiated to perfect bioplastics technology and to prove that bioplastics is a solut ion and not part of a problem.
Teknor Apex Announces NEW Monprene® TPEs
Teknor Apex Announces NEW Monprene® TPEs with 60% Post-Consumer Recycled Content, Reducing…