CHINAPLAS: ENGEL to demo the production of complex LSR products in large quantities
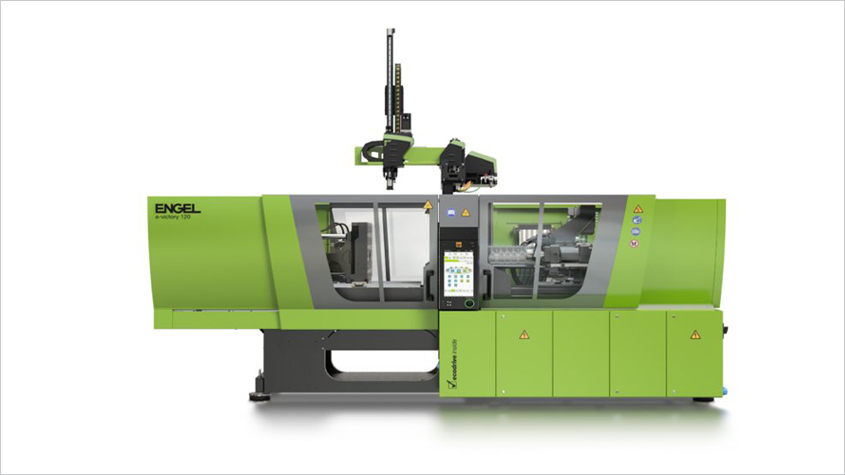
ENGEL will demonstrate how geometrically highly complex liquid silicone rubber (LSR) products can be manufactured economically in large quantities at CHINAPLAS 2019, by manufacturing LED headlamp lenses on a tie-bar-less ENGEL e-victory 310/120 injection molding machine in an automated, rework-free process.
During the four days of the fair, ENGEL will be processing Dowsil MS-1002 Moldable Silicone by Dow Silicones (Wiesbaden, Germany), a material developed specifically for use on injection molding machines. The curing speed has been optimized to obtain a smooth and very hard surface similar to thermoplastic. The high light transmission ensures a very good luminous efficiency.
Tie-bar-less technology as an efficiency factor
Tie-bar-less injection molding machines offer a number of advantages for processing LSR. The fact that the robot can reach the cavities directly from the side without having to circumvent any obstacles reduces the handling time, and therefore the mold opening time.
On top of this, the tie-bar-less technology allows for particularly compact production cells. Because there are no tie bars in the way, the mold mounting platens can be fully used up to their very edges. This means that the high-volume lens mold necessitated by the complex component structure fits on a comparatively small 120 ton injection molding machine.
“The prerequisites for economically producing geometrically demanding products from liquid silicone are automated, rework-free processes as well as high precision and stability of the injection molding process,” as Gero Willmeroth, the President East Asia and Oceania of ENGEL, based in Shanghai, emphasized. “Thanks to its tie-bar-less clamping unit, the e-victory machine with an electric injection unit is predestined for this.”
Intelligent assistance prevents rejects
ENGEL has equipped the e-victory with iQ weight control for the manufacture of the LED lenses to ensure the required precision during injection throughout the entire manufacturing process. The intelligent assistance system from ENGEL’s inject 4.0 program analyses the pressure profile during injection of the polymer melt, compares the measured values with a reference cycle and adjusts the injection profile, the change-over point and holding pressure shot by shot to the current conditions.
Fluctuations in the raw material and ambient conditions are automatically compensated before even a single reject molding is produced.
The camera system integrated in the process checks and documents the quality of the parts. An ENGEL viper 40 linear robot is used for parts handling.
Augmented reality reduces errors in operation
ENGEL integrates all of the production cell components in a single control to be able to set up and control the entire process via the injection molding machine’s CC300 control panel.
In addition to automation, control integration also includes the LSR metering equipment, which, like the mold, comes from ACH-Solution (Fischlham, Austria), as well as an augmented reality (AR) solution, which ENGEL is implementing together with AVR Tech Innovations, also from Fischlham, Austria. Trade fair visitors can be guided through the individual work steps required to start the production cell with AR (Augmented Reality) glasses.
In the injection molding plant of the future, augmented reality can support machine setters and maintenance personnel with the aim of working even more efficiently and reducing the risk of errors in operation.
Connectivity ensures transparency
In Guangzhou, ENGEL will also be presenting TIG authentig for linking injection molding machines and production cells. The MES (Manufacturing Execution System) by ENGEL subsidiary TIG (Rankweil, Austria) is tailored to the specific requirements of the injection molding industry down to the last detail.
It ensures transparency in order to, for example, utilize the capacity of the machine park or correlate productivity indicators and economic objectives. The new products that TIG will be presenting in China include the TIG 2go dashboard solution, which is particularly suitable for entering the MES world, and the TIG big data high-performance analysis platform for networking machinery around the globe in a central cockpit.
Teknor Apex Announces NEW Monprene® TPEs
Teknor Apex Announces NEW Monprene® TPEs with 60% Post-Consumer Recycled Content, Reducing…