Additive Manufacturing: 3D printing at the fore
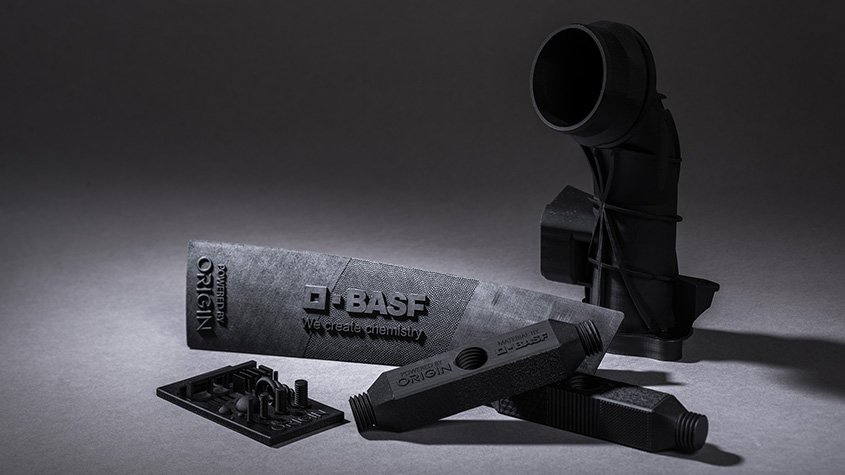
Additive manufacturing or commonly known as 3D is seeing a spurt of growth with various companies making announcements for new tie-ups and product launches to make the process more commercial for mass production.
Collaborations for technologies
German chemicals firm BASF’s 3D Printing Solutions unit is to provide its photopolymer additive manufacturing materials to Paxis for its new WAV (Wave Applied Voxel) technology, created with the end-user firmly in mind in an effort to solve trapped volume issues of within current liquid resin-based technologies.
BASF’s Ultracur3D ST 45 reactive urethane photopolymer has been designed for high accuracy and mechanical strength, where existing 3D printing materials often reach their limitations. Ultracur3D ST 45 can be used to produce functional parts by using a wide variety of equipment, such as stereolithography (SLA), digital light processing (DLP), or Liquid Crystal Display (LCD).
Paxis’s primary focus is commercial manufacturer applications in the aerospace, automotive, dental and medical sectors, as well as identifying potential vertical markets within advanced manufacturing that have so far been ignored due to the limitations of existing technologies.
“Pairing innovative materials at the earliest stages of designing the WAV technology is critical,” explains Mike Littrell, CEO/Founder of Paxis. “Too often, the material is modified to work within the limitations of existing technologies,” he says, adding that developing the materials prior to launching the WAV technology will enable end-users to integrate the technology quickly into their operations.
BASF has also collaborated with Origin, an openplatform additive-manufacturing printer provider, with ECCO, a footwear manufacturer, to develop a new approach to footwear production. The Danish ECCO group, using Origin’s newly developed printing system with BASF’s Ultracur3D material at its R&D Centre in Denmark, says the initial results demonstrate detailed accuracy and mechanical stability.
Paving the way for 3D to overtake injection moulding
Meanwhile, Germany’s Evonik and Evolve Additive Solutions have announced a joint development agreement where the companies will work together to formulate Evonik’s thermoplastic materials to be used in Evolve’s STEP (selective thermoplastic electrophotographic process) additive manufacturing solutions. The initial development efforts will focus on PA12, PEBA (polyether block amide), transparent polyamide, and polymers from the PA6 series. In the future, the combined efforts will result in a wider range of materials for STEP users with more 3D printing material choices for production that are commonly used in traditionally manufactured products.
Once commercial, Evolve’s STEP technology will sit alongside traditional manufacturing processes, such as injection moulding on the manufacturing floor, augmenting an organisation’s production capabilities and allowing freedom of design and faster time to market with “tool-less” production. The selective thermoplastic electrophotographic process from Evolve is still in the alpha development stage and is expected to be commercial in late-2020.
“STEP has been developed for volume manufacturing so offering the widest range of thermoplastic materials to our customers is a critical element for production,” said Steve Chillscyzn, CEO of Evolve Additive Solutions. “The joint development agreement with Evonik allows us to broaden the spectrum of STEP materials to include materials currently accepted by OEMs from additive manufacturing, but more importantly to debut a whole new set of materials opening up more applications that can take advantage of everything additive manufacturing offers.”
Developing new materials for the market
Belgian chemical firm Solvay is working with Stratasys to develop new additive manufacturing filaments for exclusive use in Stratasys’s FDM F900 3D printers. The companies will develop a filament based on Solvay’s Radel polyphenylsulphone (PPSU), meeting stringent compliance requirements for use in aerospace applications.
Commercialisation will be in 2020 and additional highperformance products meeting industry-specific needs in other key AM end-use markets will follow.
Meanwhile, Dutch chemical firm DSM, which invested in additive resin supplier Adaptive3D early this year, will sell Adaptive3D’s newest product, Soft ToughRubber, a new 3D printable photopolymer.
The new material is said to allow manufacturers to explore applications in medical models and consumer products such as audio earbuds and footwear. The partnership will guarantee the availability of the new material in production volumes worldwide.
The material combines the feel and mechanical properties of silicone with the resolution and surface finish that Digital Light Processing (DLP) printing provides.
DSM and Adaptive3D also say they will continue working together closely to explore new applications and develop materials that best meet market needs.
Yet another company, Elix Polymers, a supplier of ABS materials, has added two new grades to the Ultimaker Marketplace for 3D printing equipment FDM applications. The move was made together with three partner companies producing filament from Elix ABS: 3R3D, based in Spain; Filoalfa brand owner Ciceri de Mondel (Italy); and Print-me (Poland). The companies in the partnership cooperated within the Ultimaker Material Alliance Program.
The two new ABS grades are 3D-FC and ABS 3D-HI. The 3D-FC material is certified for medical and food contact applications, complying with the ISO 10993-1 and USP Class VI standards determining biocompatibility. Certification covers the whole material recipe, including colour pigments (the material is available in different colours).
The second grade is a high-impact ABS grade with lower density than other ABS grades and offering high impact resistance, even at low temperatures, says Elix. Impact performance is comparable with ABS/PC, which has a higher density, making the new grade particularly suitable for automotive applications where weight-saving is an issue.
Possible applications include functional prints of prototype parts (assembly tests in automotive, for example), industrial/medical tooling (jigs and fixtures), and short series of personalized parts.
With traditional injection moulding customers now starting to adopt Ultimaker 3D printers, the companies expect a good take up rate and opening up of new applications for 3D printing.
Ultimaker – a global leader in desktop 3D printing – had earlier announced that its Ultimaker Material Alliance Program had already influenced over 80 companies worldwide to develop material print profiles for FFF 3D printing.
The programme was launched a year earlier to meet the growing demand for industrial-grade engineering 3D printing materials.
Ultimaker says its Print Profile Assistant is being adopted to rapidly bring a wide variety of highperformance FFF 3D printing materials to the professional market. These material print profiles become available for download in the Marketplace in Ultimaker Cloud.
KraussMaffei showcases pioneering Additive Manufacturing solutions at formnext
precisionPrint stereolithography 3D printer show smultilaser-technology for series product…