Electronics/electrical Industry: The ultrathin wonders of printed electronics
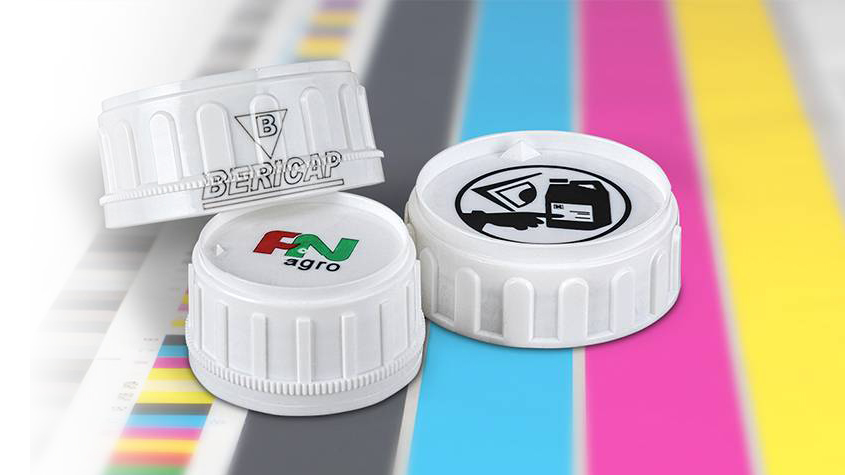
Products and brands are harnessing the enormous potentials that are packed within the wafer-thin shell of the printed electronics technology, says Angelica Buan in this report.
The effusion of technology advancements in consumer products has set off a criterion that thinner is better and less is more. This is the case in the deployment of printed electronics in products that have also evolved over time and based on consumer preferences.
Printed electronics are thin, lightweight, and flexible technology that can be printed with conductive inks on large area substrates, such as plastics, paper, glass or textile. One benefit of printed electronics is that they can be produced at a low cost.
Moreover, printed electronics enable consumer products to be more compact, more interactive, and more mobile, to cite a few advantages. This is a paradigm to future proofing technology-driven industries. Flexible screens, smart labels
and packaging, sensor-enabled materials, batteries and more are now being equipped with printed electronics.
While printed electronics are relatively at an early stage of development, the sector is projected to gain traction fast, driven by demand for thin, robust, and flexible substrates that provide secure and cost-effective and significant cost advantages from high growth in industries including the automotive and mobility, IoT (Internet of Things), healthcare, consumer electronics, printing & packaging, and building & construction.
Breakthrough application in 5G technology
Boasting to be hundred times faster than current network speeds and higher reaction times, 5G or the fifth generation standard is heating up the devices technology arena. 5G, which requires use of unoccupied, higher-frequency bands (26 GHz and above), is predicted to see a surge of applications in mobile devices, machines and technologies; enabling not only person-to-person communication but also connected devices communication. An important component in advancing 5G technology is printed electronics.
The Communications Research Centre (CRC), Canada’s advanced telecommunications research centre, is collaborating with the National Research Council (NRC) of Canada, and human machine interface technologies manufacturer GGI Solutions to advance the use of engineered surfaces with printed electronics in nextgeneration mobile wireless communications.
CRC and NRCC are both members of intelliFLEX, a notfor- profit industry alliance in Canada, aiming to accelerating the growth of the flexible and hybrid electronics sector of more than 300 organisations across the country.
Researchers at the CRC are using engineered surfaces to control the propagation of electromagnetic signals in a wireless communications environment. One of the enabling fabrication technologies is printed electronics. It explained that by printing metals and dielectrics (an additive fabrication process), engineered surfaces can be incorporated in existing building materials such as wallpaper, or drywall, in a low-cost, high-volume, and readily commercialised manner.
Improving wireless coverage using these materials would be much cheaper than installing additional cell towers or repeaters. Eventually, this concept could be used in designing new buildings, or even in the building codes to plan for wireless coverage in a similar way as heating and cooling is today.
Collaboration to step-up connected mobility
Market researchers are of a similar mind that the printed electronics market is poised for billion dollar growth as it matures over time. Markets and Markets estimated the printed electronics market to double by 2023 to US$13.6 billion from US$6.8 billion in 2018, registering a CAGR of 14.9%.
Printed electronics are gaining high traction worldwide owing to the rise in the application in IoT. In part, it is also driven by the synergistic efforts of companies to develop better versions of the technology.
Printed electronics are suited in concept cars with connectivity capabilities. Novares Venture Capital Fund of the France-headquartered global plastics solutions provider, Novares, has recently acquired a minority stake in European printed flexible electronics specialist, Quad Industries, to develop new systems with intuitive intelligent interfaces for all passengers, and add to Novares’s solutions for cars.
Novares’s investment is part of a development partnership forged between the two companies in May 2018 that are collaborating on advanced user experience projects within Novares’s open innovation lab, the Nova Car. Quad’s technology is already integrated in the Novares “Touch’N Play” concept, incorporated in the Novares demo car.
Novares and Quad are working on even more solutions with intuitive intelligent interfaces using 3D-shaped electronics for Novares’s second vehicle prototype, which will be unveiled in Paris in June. Future co-developments include Quad’s technologies in proximity sensing, gesture control, vital signs monitoring or stretchable sensors.
Packaging got smart-tagged
The growth of the smart packaging market is propelling the development of printed electronics in the segment. The global smart packaging market is growing at a fast rate. In three years’ time, it is forecast to achieve a CAGR of almost 8% from 2014 to US$37.8 billion, according toAllied Market Research.
Scoping into smart packaging, Bericap, Germany headquartered supplier of caps and closures, is partnering with California-headquartered near field communications (NFC) solutions provider Thinfilm Electronics to develop fully integrated digital authentication solutions for closures in over-the-counter pharmaceuticals and industrial applications.
The collaboration will embed advanced chips into the closures to create dependable and cost-effective solutions for brand protection and authentication purposes.
Thinfilm’s NFC OpenSense and SpeedTap products communicate wirelessly with NFC-enabled smartphones and can be applied to everyday objects. Thinfilm provides fully integrated services throughout the entire process incorporating NFC tags, integrating them onto products and delivering data and actionable insights via the CNECT cloud-based platform at scale.
Bericap cited two significant benefits it expects out of the partnership: security and marketing. Jörg Thiels, CEO of Bericap, said that smart and anti-counterfeiting packaging solutions are fast developing requirements and Thinfilm’s technology and software platform complement Bericap’s extensive assortment of closures (it produces over 84 billion/year plastic closures and dispensers).
Kevin Barber, CEO of Thinfilm, concurs saying that developing product closure solutions will help stop the global proliferation of product counterfeiting, refill fraud, tampering and diversion.
Elsewhere, US speciality paints and coatings manufacturer PPG Industries and US RF-based wireless power technologies provider Powercast Corporation have recently sealed an agreement to jointly develop ultra-thin and wirelessly powered printed electronics products. The advanced solutions combine PPG Teslin substrate, PPG conductive inks and Powercast’s Powerhavester receiver technology for delivering over-the-air wireless power.
Powercast and PPG will introduce LED-based wireless illumination solutions for smart consumer packaging and smart identification (ID) cards, which enable enhanced security. With this technology, smart consumer packaging lights up to showcase products on a shelf. Smart ID cards also illuminate to permit or deny access to restricted areas or to verify user credentials.
The companies’ combined technologies allow developers to seal electronics into packaging and cards via lamination to provide indefinite illumination without wires, batteries, charging ports or direct contact with a power source.
The application is piloted in the packaging of Straub Brewing’s six-pack beer. A PPG Teslin label is affixed to the front of the six-pack packaging to illuminate it and draw attention to the Straub brand. A subsequent application is a smart ID card that authenticates a user based on proximity to an ID reader.
The PPG Teslin substrate is a microporous synthetic paper with the ability to cushion printed electronic circuitry while able to withstand handling and abuse typically associated with credential and packaging applications, according to PPG.
Meanwhile, PPG says its thick film conductive inks are formulated to meet a wide range of printed electronic circuitry applications, including printed radio-frequency identification (RFID) and mobile antennas, membrane switch and capacitive touch panels, flexible OPV solar panels, printed sensors and medical biosensors.
In the healthcare space, Germany-based speciality pharmaceutical labelling solutions provider, Schreiner MediPharm, likewise has struck a collaboration deal with German packaging specialist Edelmann to develop a demo version smart medicine packaging solution with diverse digital features, including the BitSecure copy detection technology for product authentication. A closure seal with an integrated NFC chip (which can be read using a smart phone and a related app) and a void effect for tamper evidence also have been incorporated.
The BitSecure copy detection technology is a printed, digital security feature based on a high-resolution, random pattern whose intricate details are not discernible by the naked eye, explained Schreiner MediPharm.
Market lighting up for printed OLED
IDTechEx Research projected that the printed, flexible and organic electronics market will cross US$31 billion in 2018. However, with the increasing demand for these novel electronics, their commercial growth could sky-rocket sooner than predicted. Foldable and printed OLED (organic light-emitting diode), distinguishable from its predecessor for its ultra-thin, transparent and flexible characteristics, is becoming a thing in various applications, such as consumer goods, automotive and more, and continues to open up more new market opportunities.
European research project PI-SCALE recently introduced a prototype for a light art object created by EMDE development of light GmbH with product designer Christoph Petersen. The Colorloop prototype demonstrated the application possibilities with flexible OLED.
The PI-SCALE project, launched by the EU in 2016, and branded as Lyteus, establishes a European-wide roll-to-roll flexible OLED lighting pilot production line, with an aim to enable companies of all sizes to quickly and cost effectively test and scale up their flexible OLED lighting concepts. At its launch, Lyteus has served four customers, namely, Audi, Rehau, EMDE and Pilkington to develop flexible OLED lighting products in the automotive, aeronautics and designer luminaires sectors.
Lyteus partners include Holst Centre/TNO, UK CPI, Fraunhofer FEP Institue, VTT, BOM, DuPont Teijin Films, Coatema, FlexEnable, M-Solv, FE, and Amires.
For Colorloop, EMDE worked with research partner VTT from Finland, which developed a battery-powered driver with programmable control. The transparent and flexible OLEDs come from Fraunhofer FEP in Dresden, Germany.
Meanwhile, flexible OLEDs are also targeted for product packaging. Lyteus, exploring this possibility, developed a flexible OLED panel embedded in the paper label, which lights up to display the logo on a product bottle. The OLEDs can be printed to produce any shape or colour, and can be used to highlight specific product details, such as a drink’s flavour or colour, or to provide additional information. The lighting may be activated in several ways, for example, when the package is touched or when the product is opened; or may react to temperature or sound.
The OLED panels are incredibly thin, just 330 microns thick, making them ideal for embedding into paper labels. They are also very flexible, so can be easily bent for curved objects like a bottle or cup.
Currently, production of the OLED labels is based on a sheet-to-sheet process. For mass manufacturing for labels, the process needs to be scaled up to be able to produce large numbers of labels consistently.
Holst Centre, an independent R&D centre that develops technologies for wireless autonomous sensor technologies and flexible electronics, is developing a roll-to-roll pilot production process to address the challenges of producing OLED labels in large quantities.
The Dutch company is further developing the technology for labels. For example, the current implementation still needs wires and a cell battery. These could be replaced in the future with flat, flexible batteries or even flexible wireless charging coils. And it may eventually be possible to integrate flexible OLED displays, providing even more possibilities for attracting and informing customers about products.
Similarly, multinational beverage manufacturer Coca Cola Company is exploring into this direction. In a promotional campaign called #BeSanta, launched in December last year, OLED technology was applied to a limited edition batch of 330-ml glass bottles of the drink product, to make the Coca-Cola logo light up when touched
The technology came from Berlin-based OLED specialist, Inuru. Accomplishing the labels, Inuru worked with German labels and flexible packaging manufacturer, All4Labels, and used conventional inks and printing technology to produce pressure-sensitive paper labels bearing all the typography and colours of a Coke label.
Georgi Blaskov, Senior Brand Manager Coca-Cola CEE, see that future developments to bring the cost down are encouraged to make broader commercial application of printed electronics technologies, such as the flexible OLED, particularly in promotional mainstream packaging activities.
Meanwhile, All4Labels is optimistic about making this technology as cost efficient as possible. The Berlin company produces inks that allow the printing of thin OLEDs with standard industry printing equipment. It has, thus, the potential to scale the production of low cost label electronic devices to billions of units.
KraussMaffei showcases pioneering Additive Manufacturing solutions at formnext
precisionPrint stereolithography 3D printer show smultilaser-technology for series product…