South Korea: No stopping Asia’s master of innovations
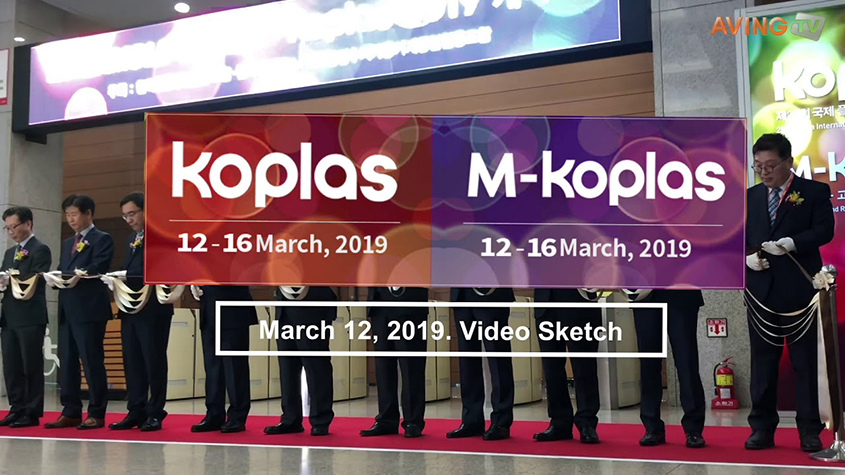
South Korea is leaving no stones unturned to further mature a technology-driven industry, says Angelica Buan in this review of the recently concluded Koplas 2019 show, held 12-16 March in Seoul. The show spanned an area of 26,487 sq m with 4,300 booths occupied by 1,280 exhibitors. The total number of visitors over the five days was 85,016, with 2,417 from overseas.
Charting Industry 4.0
South Korea has secured the top spot in innovation charts and has been cited the world’s second most innovative country after Sweden, according to the 2018 Bloomberg Innovation Index. This is not surprising as the world’s 15th largest economy is also the world’s top producer of mobile phones, semiconductors, displays, and vehicles loaded with the latest bells and whistles in connected mobility.
As a strong contender in the advanced manufacturing arena, South Korea is actively adding on mileage to its Industry 4.0 (i4.0) blueprint to even up with its East Asian counterparts. The latter include Taiwan that is in a similar pursuit of forming a smart manufacturing framework; Vietnam, which is expanding the use of robotics on the manufacturing floors; China, which wields connected technology infrastructure in line with its One Belt and Road initiative and the Made in China 2025 manufacturing roadmap; and Japan, which has made a giant leap to what it calls Society 5.0, or the Super Smart Society that is epitomised by application of AI, big data, Internet of Things (IoT), and robotics.
In the years to come, South Korea will be seeing its manufacturing industries become digitally driven. By 2022, it intends to build 30,000 smart factories and ten smart industrial zones.
Obviously, adoption for i4.0 has the potential to further increase, based on an audit undertaken by the Bank of Korea in 2018. Of the 272 manufacturers taking part in the survey, more than half were of the opinion that the transformation is vital and thus are taking measures to adapt to the i4.0 concept. The sectors that are found to be more coalescing to a digital technology-based manufacturing setup are the automotive, petrochemicals, and information technology; while the steel, shipbuilding and machinery equipment sectors are following suit.
Meanwhile, there is not a lack of companies that are taking interest in South Korea’s advanced manufacturing thrust, as viewed at the recent industry exhibition, Koplas 2019, which showcased a fete of technologies to demonstrate the readiness of the South Korean in smart manufacturing, a key component of i4.0.
Organised by Korea E & Ex and the Korea Plastics Processing Machine Industry Cooperative (KPPMIC), Koplas had exhibitors from 27 countries.
Tying up for further presence
South Korea is among the world’s major bailiwick for automotive innovation, yet is on the verge of being outperformed by other vehicle producing countries such as India, China and Mexico, in terms of production and sales.
Based on data from the Korean Automobile Manufacturers Association (KAMA), automotive production fell 2% to slightly over 4 million vehicles in 2018 from a year ago. Big automotive makers that have bases in South Korea are moving production elsewhere, like Hyundai Motors setting up in Mexico and India, and General Motors, which has opened a sales office in Incheon, sold its factory in Gunsan to Gyeongsan-based Myoungshin.
Thus, to balance out the automotive industry’s lukewarm performance, South Korea is looking to other areas with high growth potentials for its i4.0-ready industries.
In view of this, Italian auxiliary equipment company Piovan has started a partnership with local company Toba, to boost its presence in the country. “We want to increase sales, and at the moment are officialising a commercial partnership with Toba, a key player in South Korea’s plastics industry,” said Federico Ruzzon, Sales Director of Piovan (China). Toba supplies factory automation, pneumatic conveying systems and smart factory systems, to name a few.
Ruzzon explained how South Korea’s smart factory readiness matches the company’s offerings. “We are serving customers from Italy. Smart factory, being the key point both for Piovan and Toba, bridges the distance between our headquarters and our Korean customers,” he explained. Piovan’s machine system for supervision and control is Winfactory 4.0, a digital supervision software for productivity and quality.
Tuning into a no-waste concept
One of the significant elements of the i4.0 concept is its support of the circular economy agenda, which is minimising waste and recovering value of end of life resources.
South Korea, ranked fourth in UK consultancy Eunomia’s solid waste recyclers, is able to maintain high recycling rates. The only non-European nation in the top five ranking in 2018, it achieved a nearly 54% recycling rate. This is also in the face of China’s ban on solid wastes from other countries entering its borders.
Having said this, it is expected that industries in South Korea will be benefitting from recycling technologies, not only to increase solid waste recycling rates but also to give emphasis to the value of circularity.
This was also the opinion of Koplas exhibitor Austria-headquartered recycling machine maker Erema, which displayed the Regrind Pro technology.
Fritz Josef Wimmer, Head of Sales (Asia, Oceania, CIS and UK), said that the new technology focuses on post-consumer plastics.
“The application of this machine has not caught up in South Korea until now since post-consumer materials have to be produced by countries affected by the China waste ban,” Wimmer said.
The RegrindPro processes PE, PP, ABS or PS plastics and other regrind types into pellets. Typical regrind sources are packaging, automotive applications, waste electrical and electronic equipment, household, building/construction, and more.
Wimmer added: “South Korea is a high-priced country, and so to run factories more economically, implementation of i4.0 compliant machines is necessary.”
True enough, this is the trajectory of the industry as it looks further ahead to the prospect of becoming the region’s paradigm for advanced manufacturing through persistent innovation and technology development.
Exhibitor Maag Systems Singapore, the Asian sales arm of Switzerland-headquartered gear pumps, pelletising and filtration systems manufacturer Maag, promoted a range of pelletisers that allow reusable waste from injection moulding to be recovered and recycled into a finished product.
Seah Poh Siang, Sales Leader Asia, described the pelletising technology as i4.0 compliant, suited for South Korea’s packaging, profile and other industrial applications. He added, “The plus points of Maag’s pelletisers are the energy efficiency and compact design.”
Niche for efficiency in plastic processing machines
Coveting the energy efficiency and just-in-time manufacturing advantage to meet demand sans wastage, German machinery maker Dr Boy, along with its representative Scientific Chemical Machinery (SCM), displayed the vertical 100 kN Boy XSV machine overmoulding metal nail files; and 63 kN-Boy XXS shown producing bookmark clips.
Both machines are equipped with 3D-printed mould inserts. In this way, injection moulded parts are produced, which have the same physical properties as if they were produced with conventional moulds. This is not possible with the additive component manufacturing on 3D-printers. By using printed mould inserts, plastic parts from almost all materials, even glass-fibre reinforced plastics, can be processed and cost-effectively moulded even in very small quantities.
The printed mould inserts are said to be a more cost-effective alternative to traditional metal moulds for the use in prototype manufacturing and small batch production.
Market growth for companies
Ruzzon of Piovan described the South Korean market as a matured, high-level market. “South Korea is an important market for us as there are a lot of opportunities where we can offer our quality, stability, reliability,” he furthered.
Christian Sorz, Project Manager of Boy attested to the positive demand for plastic processing machines and solutions in the market, with the company seeing increasing sales.
German compounder Kraiburg TPE is meeting the growing TPE demand in Asia Pacific for key markets with the set-up of Kraiburg Rubber (Korea), its fifth local representation in the region after Kuala Lumpur, Bangalore, Hong Kong and Shanghai.
Exhibitor Wittmann Battenfeld Korea also disclosed increasing sales of its micromoulding machines in South Korea. The Gyeonggi-based subsidiary pegged about a 40% rise in domestic sales, according to Managing Director, Chong Geun Kim, who also did a presentation on LSR/micro LSR part injection moulding during the technical seminar at Koplas.
There is a robust demand for injection moulding machinery from the South Korean market, with the total market volume estimated at 2,000 machines/year with about 30% of this volume delivered directly to South Korea and the remaining 70% being required by companies for their facilities outside South Korea, concluded Wittmann Battenfeld.
KraussMaffei showcases pioneering Additive Manufacturing solutions at formnext
precisionPrint stereolithography 3D printer show smultilaser-technology for series product…