工程塑料——更坚固耐用的塑料
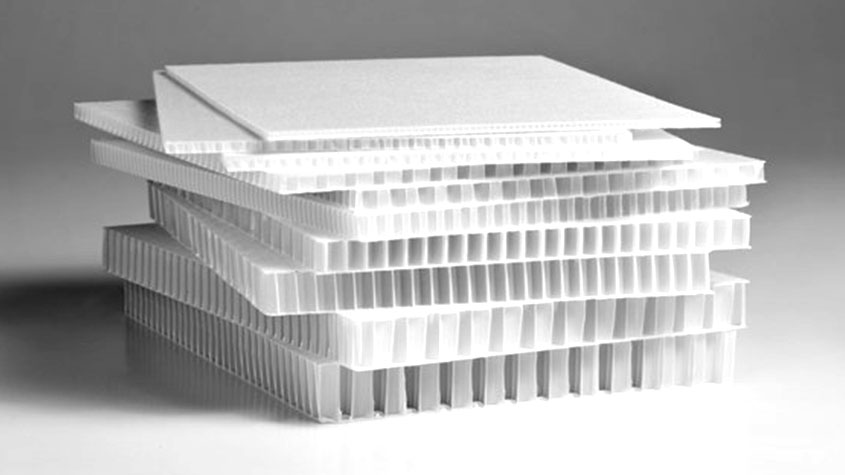
根据Angelica Buan的报导,工程塑料,比标准日用塑料更加坚固一倍,凭着更强大的机械和热力特性,正逐渐征服汽车和航空航天领域。
工程塑料是一种热塑性塑料,具较高的冲击强度和耐磨耗特性;耐磨损、耐化学和耐疲劳;与商品材料相比,它能够抵御极端的环境条件。汽车及运输、建筑、航空航天、医疗保健等主要行业正在推动使用工程塑料,其中包括尼龙、ABS、PC、PEEK、PBT和POM等聚合物。
根据Markets and Markets的报告,从2016年至2026年,全球的工程塑料市场的复合年增长率将达到7.4%,接近1090亿美元,这一点并不让人感到意外。快速增长的城市化,基础设施发展和增加的可支配收入是推动全球的工程塑料市场增长的几个令人信服的因素。
汽车:工程塑料的先驱者
全球的汽车工业蓬勃增长,带动了工程塑料的发展,其中亚太地区占据了极大份额,特别是印度、中国、日本和韩国等国家的主要汽车市场。
随着自动驾驶、汽车动力传动系统电气化,以及新的物流概念等新形式流动的快速发展,PA6、PA66和PBT聚合物的应用潜力也日渐扩大,特别是在轻量化设计、充电系统、电池解决方案,自动驾驶和电动机外壳使用的传感器,以及电动汽车的基础设施如充电站。
引擎盖下方的热负载是一个热门话题。德国Lanxess公司开发的热稳定系统XTS2(极限温度稳定),可将PA66的热稳定性提高至230°C。 XTS2产品组合中的第一款产品是35%玻璃纤维增强PA66 Durethan AKV35 XTS2。它非常适合用来生产拥有集成中冷器的进气歧管。另外,正在开发中的30%玻璃纤维增强PA66,适用于吹塑成型的空心部件,如引擎舱内的空气管道。
美国的PA66制造商Ascend Performance Materials公司,也开发了一种耐高温PA66 Vydyne XHT,其中两种等级设计可长时间暴露于210°C和230°C的环境。
根据相关用途的要求,工程塑料可全面替代较重的金属部件,或与复合材料(如Lanxess的Tepex连续纤维增强热塑性复合材料)结合使用。通过使用轻质材料和技术,可以减轻单个部件的重量,而不会影响其物理性能,如机械强度。
美国的Teknor Apex公司表示,其新系列的Creamid A3H7.5G玻璃纤维增强PA66复合材料是一种更经济,可替代金属或现有的聚邻苯二甲酰胺(PPAs),甚至是PA4.6、PA11T、 PA MDX6或PA4T等特殊PA的替代品。该公司说,其优点在于较低的加工和模具温度,在能源消耗和模具要求方面提供额外的好处。该化合物可在280-300℃的温度和80-110℃的模具温度下加工;而PPA或PA 4.6的相应使用温度范围分别是330-350°C和130-150°C。在玻璃装载量高达60%的情况下,推荐用于需要长期高温性能的涡轮增压引擎车辆的引擎盖下方的部件。
在18个月前收购了德国Comptek的美国复合材料公司PolyOne表示,该公司现在能够提供基于PEEK、PES、PEI、PPS、PSU和PPSU等极热聚合物材料的Comptek高温配方。这些材料可取得的特性包括透明度,即使是在PSU的配方下,以及导电和/或导热性,激光标记和X射线不透明度。
另外,总部位于利雅得的化学品/塑料制造商Sabic,为电动汽车提供一项解决方案,其中包括推出一种热塑性材料,可在侧面碰撞时为电池提供保护,这对汽车制造商极为重要。 “尤其是在制造商转向需要把大型电池安装在车底板的情况下。”
Sabic说,现今的传统对策是采用多片冲压强化物来强化摇杆面板的电池保护。但是,这些金属解决方案增加了车辆的重量,并可能影响效率和行驶路程。
该公司的结构混合动力设计可利用塑料和金属制造出更轻盈的强化部件,并且改善碰撞性能。其现有的设计可提供比全金属版本低40-60%的重量,以及高达10%的能量吸收率。
此强化物为Sabic开发的一系列热塑性混合解决方案添加了生力军,它可将车辆的白车身重量减轻多达20公斤。具高温、高能量密度电介质材料的Ultem UTF120 PEI薄膜,厚度介于5微米至10微米,可提供生产轻质辅助电容器的能力,能帮助抵消电动汽车中电池组的重量。
压力下不失坚韧:飞机中的塑料
凭着高强度,高安全性和减轻重量的特点,工程塑料日愈成为航空航天工业的宠儿。
德国的航空结构供应商兼Airbus的子公司Premium Aerotec所制造的一个飞机主要结构的主要部件,是由碳纤维增强塑料(CFRP)和热塑性基体制成的。它在去年的柏林航空展上展示了A320飞机的耐压舱壁。
该部件由8个相同尺寸的部分组成,并通过焊接技术相互连接。根据Premium Aerotec的说法,热塑性塑料的可焊接性是此材料的一大优势,该材料执行了整个开发和设计的演示,而单个组件的制造是在凯撒斯劳滕与Institute for Composite Materials (IVW)合作下完成的。 Premium Aerotec透过与奥格斯堡的DLR Centre for Lightweight Construction Production Engineering的合作,开发出焊接翘曲部件的技术解决方案。
这家总部位于奥格斯堡的公司说,“与目前采用铆接铝制部件制造的传统A320系列压力舱相比,这个创先的CFRP版本质量更轻,但却具有相同的机械性能,以及更短的生产时间和更经济的制造成本。”该公司的客户群计有Airbus、Boeing 和Airbus Defence & Space。
在一项相关的发展中,美国的3D打印机和3D制造系统的制造商Stratasys,不久前推出一种名为Antero 800NA的新型PEKK,用于其熔融沉积成型(FDM)流程中,并以有意转向添加制造流程的航空航天和汽车制造商为对象。
此材料具耐化学性能,意味着它可用于暴露在碳氢化合物,如燃料和润滑剂的组件。此外,其低放气性能使它可用在卫星等密闭空间,而高操作温度性能则适合在引擎舱内的引擎盖下方使用。
采用新型PEKK作为定制或小批量添加制造比传统的机械加工流程更具优势,这是因为散装PEKK的形状和尺寸有限,并在加工过程中造成浪费。 Stratasys表示,采用添加流程,工作程序更快,并且可以允许更轻盈的部件。
在开发初期采用PEKK已经促使美国的复合材料生产商Hexcel和法国的特殊化学品公司Arkema展开一项合作,开发CFRP胶带作为生产新一代飞机的轻量化部件。合作双方将确保采用PEKK的新型复合材料的成本更低,生产速度更快。
蜂窝结构创造更轻盈特点
比利时的热塑性蜂窝芯生产技术供应商EconCore正积极地扩展其ThermHex技术功能,以生产高性能热塑性(HPT)蜂窝芯材和夹芯板。该公司已经获得PP蜂窝生产技术的许可证,并表示现正将其扩展到工程塑料,包括改性PC、PA66和PPS,以应用在汽车、航空航天、运输和建筑市场。
EconCore表示,它已在比利时鲁汶最近翻新的研发设施中成功生产并测试了多个HPT中的蜂巢。
HPT 蜂巢将建立在轻质蜂窝结构的固有优势上,帮助增加耐热性(用于电动汽车电池外壳等产品)和良好的阻燃性(对建筑面板很重要)。另外,EconCore也着手于符合铁路和航空航天应用中的FST(火焰,烟雾,毒性)规格的改良材料。该公司也在光伏(PV)面板和许多其他产品中看到巨大的潜力。
EconCore 已经展示了在新一代飞机内部模块中使用PC蜂窝的潜力。这是一项由欧洲赞助,涉及Diehl Aircabin航空公司的项目所开发的。
它还准备了一个ThermHex技术的变种,用于生产在玻璃纤维增强聚丙烯表层之间热粘合的PP蜂窝芯。这些有机夹心材料提供了获得改良的刚度与重量的比例,并且可以将它转化成最终部件 – 若有需要的话 – 也可以使用热成型及包覆成型等流程。比起较传统的复合材料和金属基解决方案,它们具备了轻量化的潜力与成本优势。
ThermHex 技术具备与各种热塑性聚合物结合使用以制造蜂窝体的潜力。这些蜂窝体的尺寸、密度和厚度可通过简单的硬件及/或工艺参数做出改变。这项工艺使它可以将表皮顺列式的粘合在蜂窝上,制作出复合夹心材料的成品。
在未来的几年,随着寻求卓越性能的新用途及新技术的出现,市场对工程塑料的需求预计也将达到新高峰。
道默化学全新现代化工厂于浙江海盐正式开业
4 月 26 日,工程材料领域全球领导者 DOMO 化学在浙江嘉兴海盐为新工厂举行隆重的落成仪式。这一重要里程碑使 DOMO 更有决心满足中国市场对 TECHNYL 尼龙材料智能解…